‘Outgassing’ in Composite Materials
Lamitex ® composites have been the chosen materials in the aerospace and cryogenic industry for many years due to their high material strength and dimensional stability under extreme conditions. When considering a composite material for spacecraft or aerospace applications it is often imperative that you take into account their outgassing properties. ‘Outgassing’ refers to the discharge of gaseous material (many times water vapor) as a result of an atmospheric change in the environment. For example; if the material or part is exposed to a vacuum or high heat. Due to the manufacturing process and nature of the base material of most laminate composites, trace amounts of water vapor and other gases tend to get into the finished product, making them ‘outgassers’ under extreme conditions. An important consideration to keep in mind is that many composite materials may contain halogens (a common flame retardant). The outgassing of halogens could be potentially noxious to humans in closed environments. We have specially designed materials, such as our Lamitex FR5, that are able to achieve flame retardant specifications without the addition of halogens - making them suitable for outgassing applications. As you can see from the table below, different composites will vary among each other in moisture absorption due to the nature of the filaments and resins used.
Testing for a material’s outgassing percentage is typically performed to ASTM Standard E595-90. The test is executed in a vacuum oven that reaches temperatures of 125C for a period of 24 hours. The sample is placed in the oven inside a container with an adjoining container connected to it to collect the displaced vapors. After 24 hours the piece is taken out and weighed (termed ‘Total Mass Lost’ –or ‘TML), along with the moisture captured (termed ‘Collected Volatile Condensable Material’ – or ‘CVCM’). An additional test that can be completed after the vacuum bake is termed as ‘water vapor regained’ (WVR). Essentially with this test, the lab attendant will leave the piece out in relative humidity at room temperature for 24 hours and then they weigh it to see how much mass was regained due to moisture absorption.
In general, materials that have a CVCM percentage less than or equal to 0.10% and a TML percentage of less than or equal to 1.00% are acceptable for space applications. However, many applications have lower standards. If the exceptional material properties of a composite are necessary, many times the end user could put the piece in a vacuum oven to expel the CVCM and then use it for their application if the material has a low WVR rate or if future WVR is not going to be an issue.
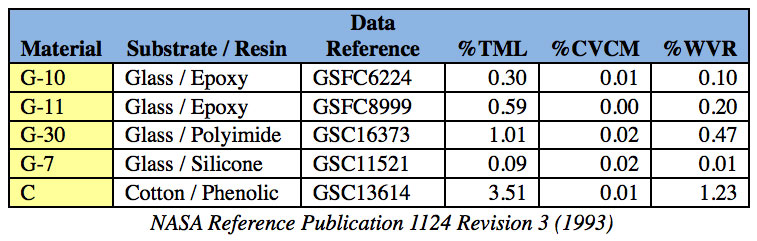