Convolutely Wound Composite tubing vs Filament wound Composite tubing: What’s the difference?
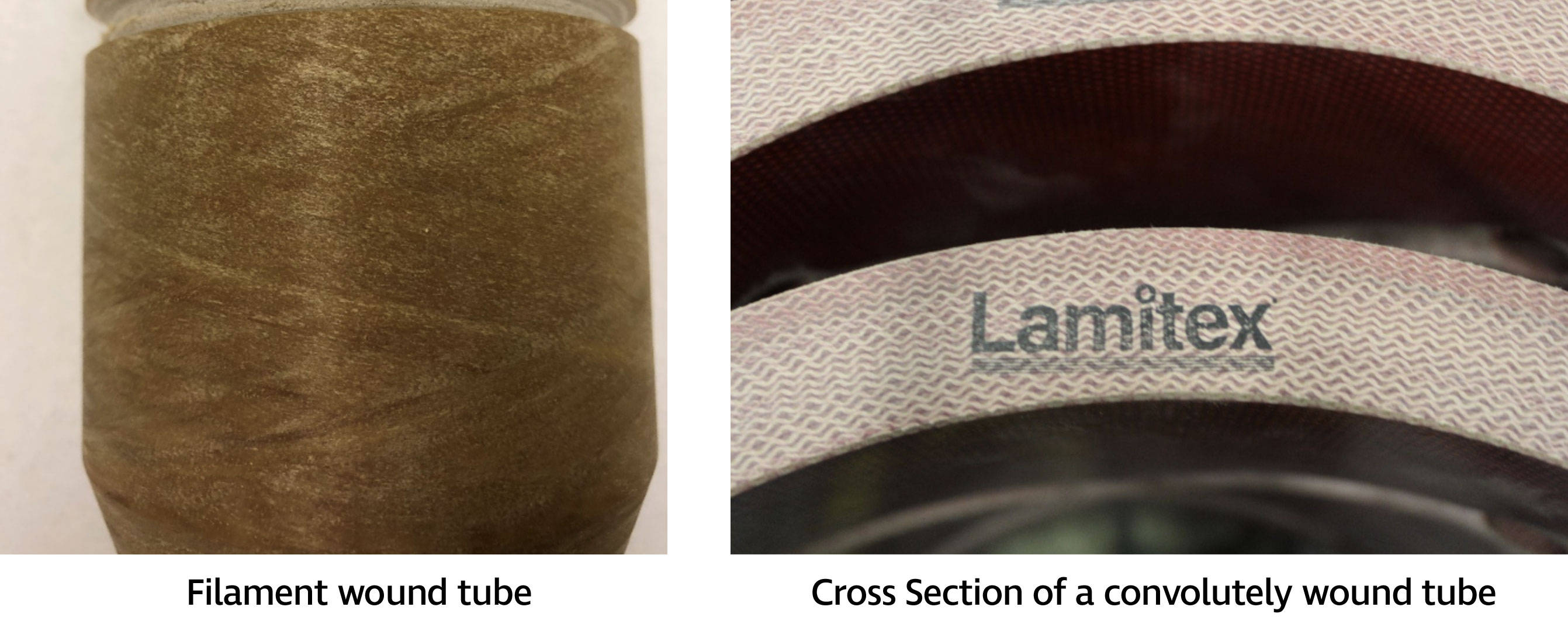
Convolutely wound composite tubing and filament wound composite tubing are two different manufacturing techniques used to produce composite tubes and each provide unique characteristics. While both methods involve the use of fiber (filament) and resin, the way in which the fibers are woven, oriented and cured can differ. Here are a few of the key differences between convolutely wound and filament wound composite tubing:
Fiber Orientation:
Convolutely Wound: Beginning with a woven prepreg (think bedsheets) that can be made from a variety of filaments including glass, cotton, polyester etc., the prepreg is helically wound around a mandrel in a continuous and overlapping pattern. The fibers are typically oriented at an angle relative to the tube axis, providing excellent torsional strength and resistance to hoop stress. Something to note: the fibers in convolutely wound tubing are not wound under high tension, allowing for more flexibility in the manufacturing process. Several Lamitex materials, such as our paper phenolic grades, are wound in this way. For a better look, visit our paper phenolic tubing page where the title video shows one being wound.
Filament Wound: In filament wound composite tubing, continuous filament(s), typically in the form of rovings or tows, are wound onto a rotating mandrel at specific angles and orientations (think fishing line on a reel). The fibers in filament wound tubing are predominantly oriented parallel to the tube axis, offering superior axial strength and stiffness. The winding angle pattern can be customized to optimize mechanical properties based on design requirements.
Manufacturing Process:
Convolutely Wound: The convolutely wound process involves a continuous mandrel rotating at a fixed speed while a fiber-reinforced, resin rich, sheet of material is helically wound onto it. The prepreg sheet is usually impregnated with a thermosetting resin such as epoxy, phenolic or polyester. This is wound continuously in multiple layers until the desired wall thickness is achieved. After winding, the composite tube is cured under high temperatures to solidify the resin.
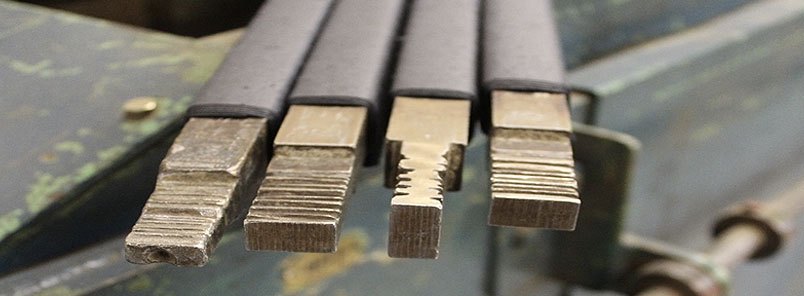
Filament Wound: The filament winding process utilizes a rotating mandrel and a creel that holds the fiber filament tows or rovings. The fibers are tensioned and fed through a resin bath or impregnation system to coat them with a resin matrix. As the mandrel rotates, the fiber is wound around it using a controlled pattern determined by the winding machine. The resin-impregnated fibers are cured either during or after winding to create a solid composite tube.
Design Flexibility:
Convolutely Wound: Convolutely wound tubing allows for greater design flexibility due to the overlapping and continuous nature of the winding process. The angle of fiber orientation can be adjusted to achieve specific mechanical properties, such as torsional strength and hoop stress resistance. Convolutely wound tubes can have various wall thicknesses along the length, and changes in diameter can be accommodated more easily. Convolutely wound material can also support smaller grooves and threads than filament wound material.
Filament Wound: Filament wound tubing can be easier to control during the manufacturing process. The angle and orientation of the fiber can be altered throughout the winding process, giving it higher mechanicals, such as hoop stress. Filament wound tubes exhibit excellent axial strength and stiffness, making them suitable for applications requiring high load-bearing capacity. Filament wound tubes can also be produced at longer lengths than convolutely wound tubes.
Mechanical Properties:
Convolutely Wound: Convolutely wound composite tubing excels in applications that require torsional strength, flexibility, and resistance to hoop stress. The overlapping fiber pattern enhances the ability to handle torsional loads and provides resistance against radial expansion. However, convolutely wound tubes may have lower axial strength compared to filament wound tubes.
Filament Wound: Filament wound composite tubing exhibits exceptional axial strength, stiffness, and resistance to elongation. The continuous fibers wound parallel to the tube axis provide excellent load-bearing capacity along the length of the tube. Filament wound tubes are well-suited for applications that demand high strength-to-weight ratio and resistance to axial forces.
Application Areas:
Convolutely Wound: Convolutely wound tubing finds applications in industries such as aerospace, automotive, robotics, and sporting goods. It is commonly used in torsional and bending applications, such as drive shafts, twistable structures, and flexible conduit systems. Convolutely wound tubing is favored when flexibility and torsional strength are critical.
Filament Wound: Filament wound tubing is extensively used in aerospace, defense, marine, and industrial applications. Its high axial strength makes it suitable for pressure vessels, structural components, propellant tanks, and piping systems. Filament wound tubes are also employed in applications requiring high modulus, dimensional stability, and resistance to axial loads.
Looking for more information about Lamitex grade thermoset materials?